BLOGS

Can One Machine Revolutionize Furniture and Architectural Design?
For decades, high frequency (HF) wood bending machines were synonymous with curved chair production. But what if this technology could transform entire living spaces? Today, advanced HF bending is answering that question, reshaping how designers and manufacturers create seamless, organic interiors from furniture to full-wall systems.
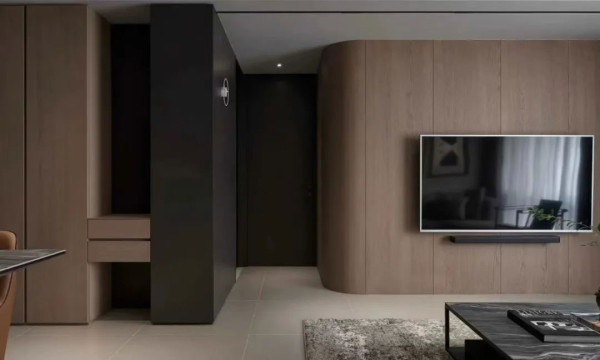
The Engine: How HF Bending Machines Work
At the core lies a sophisticated electro-thermal process:
- Dielectric Heating: High frequency oscillators (typically at 6.78MHz ) create alternating electric fields between press plates. This causes rapid molecular friction in plywood’s adhesive layers and glue moisture content, heating and curing them from within in seconds.
- Multi-Directional Pressing: Advanced machines apply pressure vertically (up to 160 tons) and horizontally (60 tons ), enabling complex 3D curves without fiber fracture.
- Instant Curing: Glues polymerize 10–30x faster than conventional methods, locking bends permanently with >80% energy efficiency.
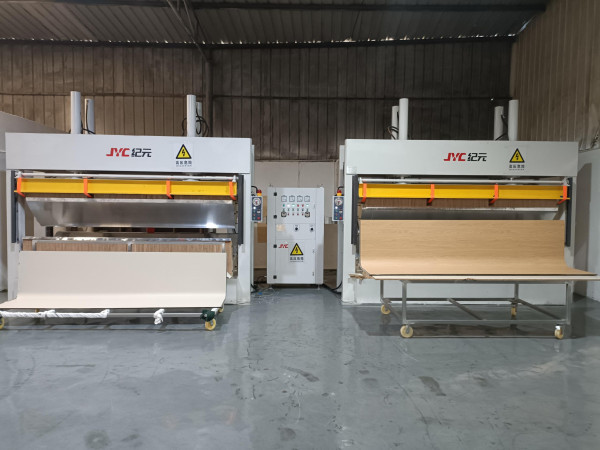
From Furniture to Full-Scale Architecture
HF plywood bending presses combine industrial robustness with precision control. These machines now transcend furniture, enabling:
- Seamless Wall Claddings: Bend plywood into flowing, joint-free wall surfaces (e.g., curved room dividers, acoustic panels).
- Integrated Architectural Elements: Produce radiused door frames, arched headers, and curved built-in cabinetry with structural integrity.
- Musical Instruments: Create elegant and beautiful shapes for guitar, violin and etc.
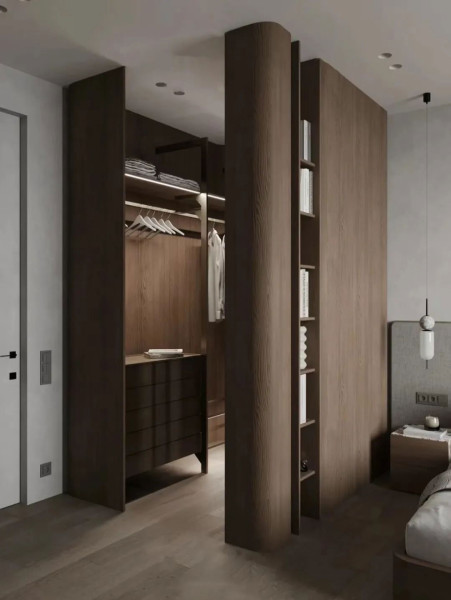
Why HF Technology Dominates Custom Interiors
1. Speed to Market
- Cure large panels (e.g., 2m door skins) in 3–8 minutes vs. hours in traditional clamps.
2. Material Integrity
- Selective heating targets only adhesive/wood fibers—no surface scorching. Curves retain 99% of plywood’s tensile strength.
3. Design Agility
- Adjust HF generators (6.78–27.12MHz) to accommodate exotic veneers, recycled laminates, or moisture-resistant adhesives.
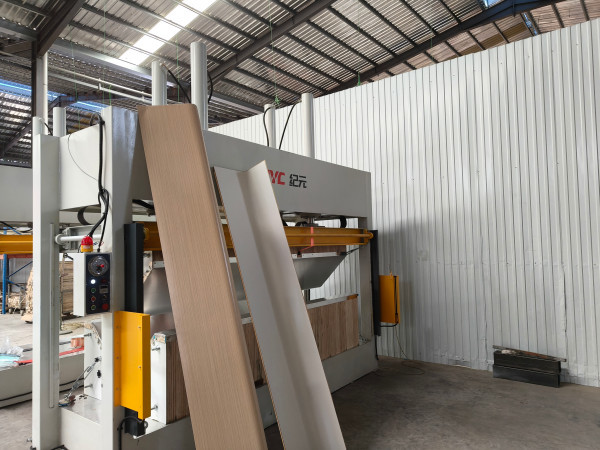
Real-World Applications Reshaping Spaces
- Unified Interior Doors: Bend door panels and frames as continuous pieces, eliminating seam failures.
- Curved Wall Systems: Fabricate radiused partitions that merge with ceilings for minimalist “pod” aesthetics.
- Ergonomic Built-Ins: Shape storage units that contour to human movement (e.g., round-edge kitchen islands, wraparound desks).
- Sustainable Production: Reduce glue waste by 65% and reject rates by 90% compared to cold pressing.
Conclusion: The Bent Revolution
High frequency plywood bending machine has evolved from a niche furniture technique to the backbone of bespoke interior manufacturing. By enabling strong, seamless curves at production speeds, it answers the growing demand for organic, human-centric spaces. As custom home markets surge, HF wood bending machines position forward-thinking manufacturers at the intersection of art, architecture, and efficiency.
Other News
China's Heading Wood Drying Solution: The Standard Setting HF Vacuum Dryer from JYC
timer :
2025-08-26
Discover JYC High Frequency Woodworking Technology at Shanghai International Exhibition 2025
timer :
2025-08-19